Morten Bach Larsen, Production Manager at Gromas Maskinfabrik A/S and his coworkers has now let a welding cobot take over a major part of the welding work. The user friendly welding robot has taken over more than half of the man hours and has proven to provide high-quality work.
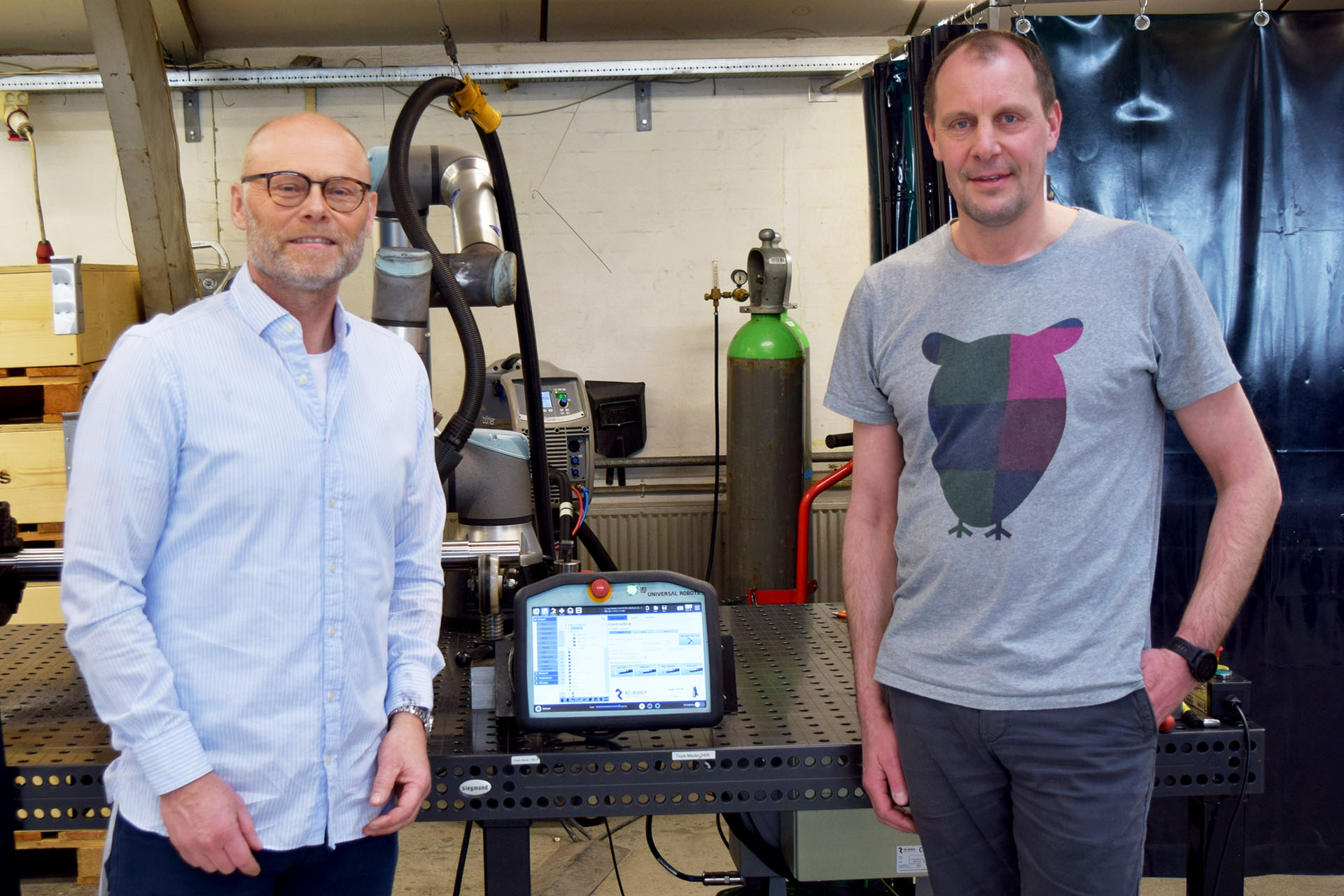
"It's not possible" was what Morten Bach Larsen was told when he started to research the market for a more efficient solution for the welding work on rotors for water pumps. He ended up finding one and has now been reassured that this was the right decision. He is now reaping the benefits of the robotic arms controlled welding movements.
Better end products
It turns out that it was possible to meet the quality expectations of the welding seams at Gromas, that is a subcontractor of the food industry. The results were acutally better than the work done manually - they simply turned out more uniform and with fewer deviations from the desired end product.
"Uniformity and the difficulty of handling the heat by hand, was something we were not able to compete with by manually welding" Morten says.
When the robot has done its job, the welders are left with a better end product and less post-processing. This is especially true for the balancers previously added:
Morten says: "We used to add 140 grams. Now, the worst ones only require 10-15 grams. The thin part of the axis, we need to be precise within 5 grams, and we normally don't see any deviations what so ever."
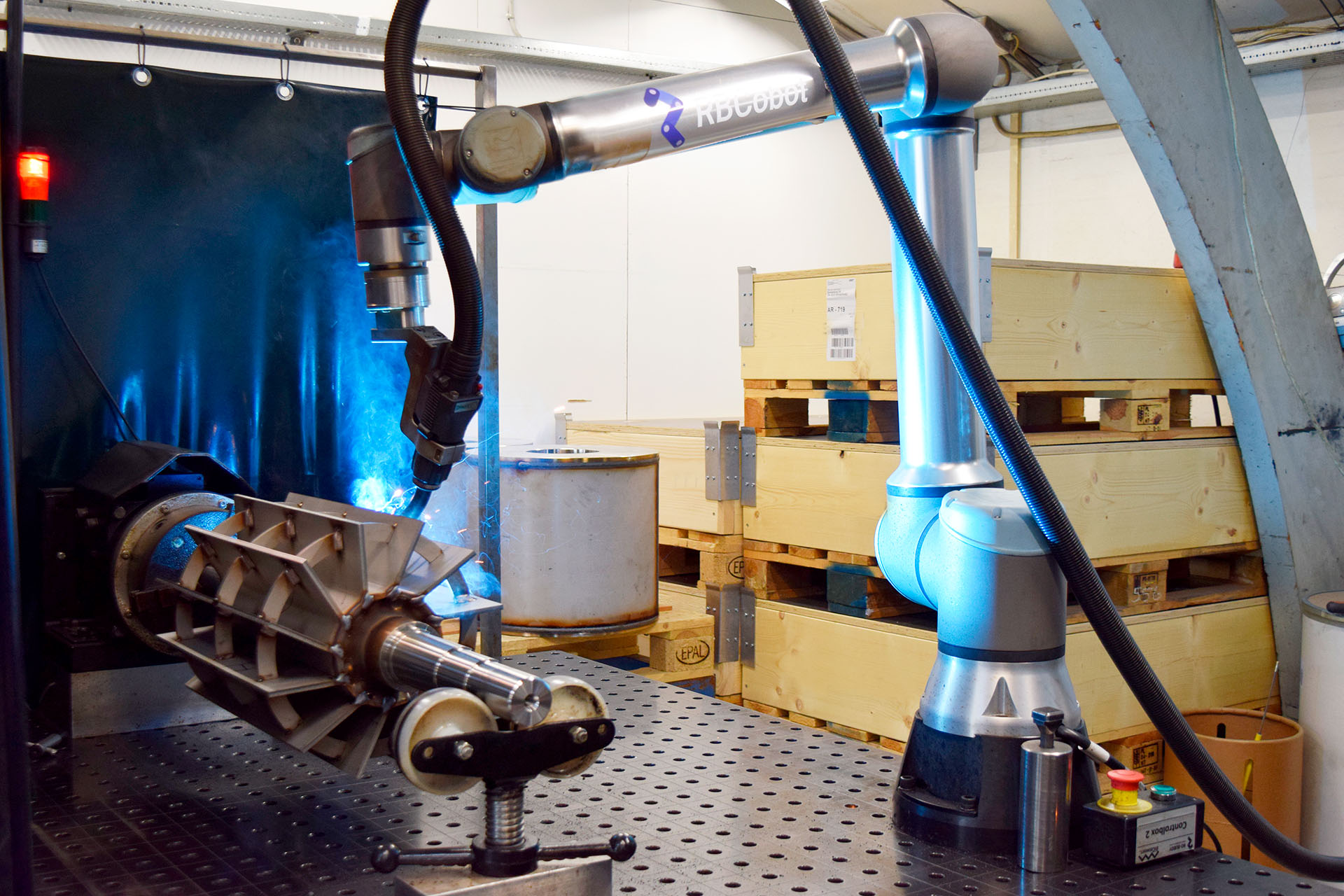
"It has freed up a lot of manual hours"
Apart from the unsatisfactory welding results, the robot was able to clearly deliver an improvement in workflow efficiency in terms of the items being weld.
When the item is ready for the turntable, the welder is supposed to activate the pre-configured program, and then the robot will take care of the rest. Afterwards, a short amount of post-processing is required, but that has also considerably been reduced.
The welding of all the seams on the pump takes exactly 52 minutes. Before the robot it took approximately 3 hours. The difference has many benefits, including to ensure the deliverabilty at Gromas:
Morten elaborates: "The automation enables us to deliver all rotators we are supposed to. We were not able to before. Before we were able to deliver 550 finished rotators per year, now we are able to deliver 800."
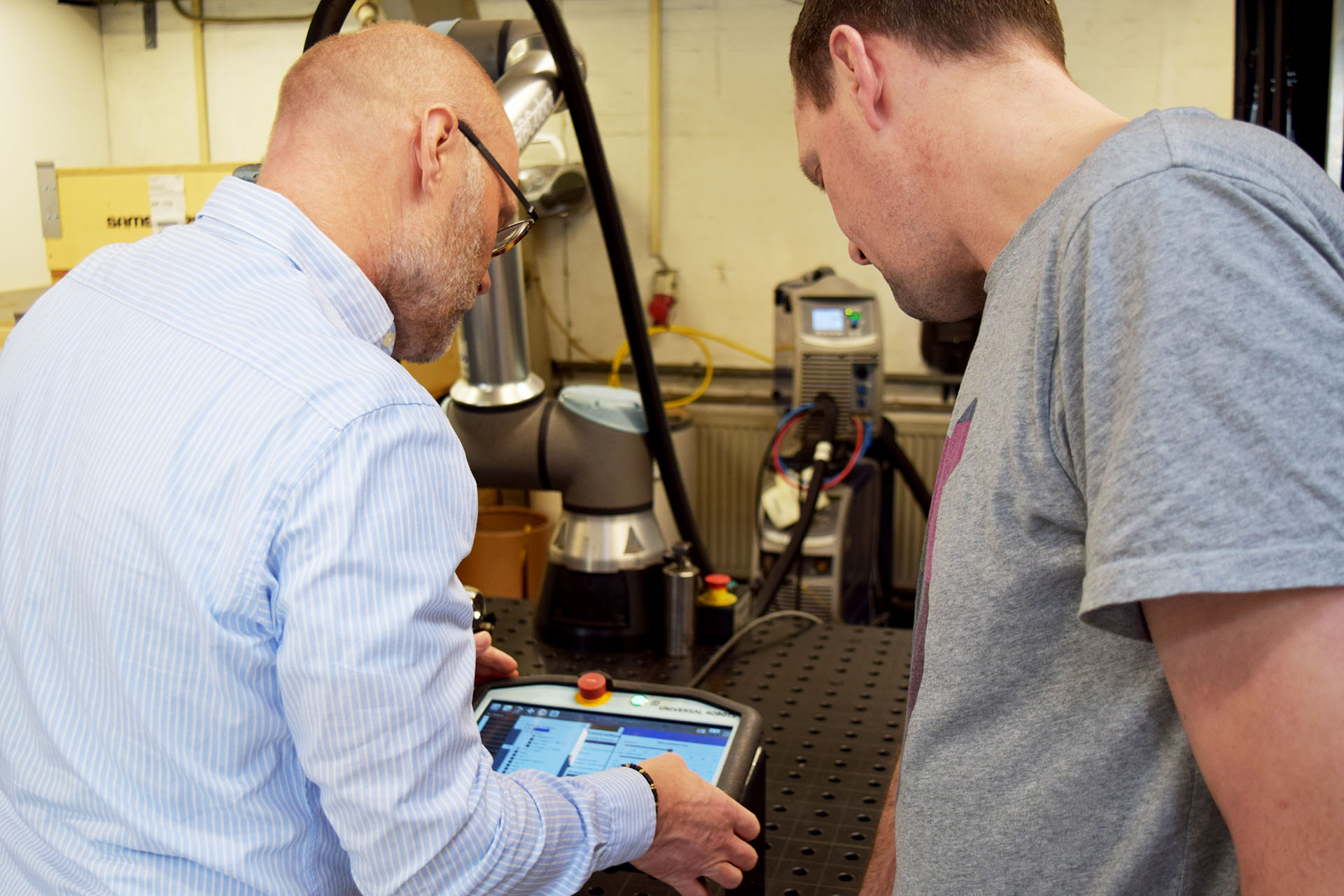
Skilled professionals behind
The workers at Gromas has welcomed their new robotic coworker, which they have now had for 1,5 years:
"It's been exciting to bring a robot in. It's nice to get new hardware, and some people have really been putting it to work." Morten says.
He points out, that the skilled workers play a vital role in following up on the development, required by the customer:
"The work put out by the robots will not be better than the input, "he says and further explains, that they have spend some time creating the right tempaltes for the welding of the pumps, which has further improved the end results.