Welding Cobots - 7 Questions Answered
Welding cobots are precise, easy-to-work-with and efficient collaborative robots specifically designed to weld. Learn more about welding cobots and what they can do for you here.
Welding cobots – What are they?
We need to first define cobots. Cobot is an abbreviation of the words “collaborative robots”. Normally, robots are just robots, where there is little to no focus on collaboration between humans. A collaborative robot, or cobot, however, is an entirely different story. Cobots are designed to work alongside humans and thus give an extra pair of hands in any given production.
Add a welding torch and a welding machine to that equation and you have a welding cobot. The basic premise of a welding cobot is that it can produce steady and precise welding results. This makes for an excellent companion in industries where large serial productions and precision are key to a satisfactory result.
From a practical point of view, a welding cobot has a two primary parts: a robot arm and a power source. This makes for a welding cobot, but more is often needed to complete the setup. E.g. RBCobots have a robotic arm from Universal Robots, a power source from Voestalpine Böhler, a welding table from Siegmund, a welding torch from Dinse and an interface-kit to ensure correct communication between the robot and welding machine. These parts cannot stand alone and are therefore integrated together by the proprietary software by RO-Buddy. The software (also called the URCap) is what makes everything work together seamlessly.
Who is a welding cobot for?
As stated previously, a welding cobot is especially useful if you produce larger series of items that require welding. Therefore, we often see manufacturers of various industrial products use the welding robot with great success. Though we also often see great results in companies that work with various types of metals in general. Particularly in industries such as the medicinal or the food industry, where precision and quality of welds are important, welding cobots can make a lot of sense. However, there is also significant benefit even with smaller series, because time spend programming is low, due to the intuitive interface.
Furthermore, schools also seem to take notice of the welding robots, as they want to prepare students for the future of welding, which very well might be a welding robot that they have to operate, at some point of their career. Furthermore, the upcoming generation of blacksmiths are not interested in backbreaking and monotonous work. They would much rather spend time perfecting their craftsmanship. Therefore a welding cobot is also a sensible addition to technical schools, who want to prepare students for a near future.
Are they safe to work with?
Many will argue, that adding a robot into a manufacturing process will make for an unsafe work environment. However, advances in the technology behind robots prove this wrong, mainly due to the integrated safety functions in Universal Robots robot arms. They will stop once they sense an external force greater than a certain value and force the robotic arm to stop. Secondly, the control boxes in the RBCobot package have an integrated emergency stop button. Furthermore, RBCobots offer easy simulations of moves, so you can get an idea of the movements before activating welding.
So in short, yes. Welding robots are safe to work around with if you know the basics of welding safety.
TIG or MIG cobot welding?
Selecting the right welding process for a cobot welder is an important choice to make. MIG, or Metal Inert Gas, is often used when the items to weld are thick and voluminous.
On the other hand, TIG-welding is more appropriate when items require more precision. The trade-off here, is that TIG-welding is a bit slower.
TIG-welding is often used when precision is more important. It uses an entirely different process, which enables the more precise weld.
An RBCobot is configurable to both options, so you are not limited to either.
Why is a welding cobot a good idea?
There is a couple of good reasons for getting a welding robot. Here we will highlight a few of them.
Increase in productivity
The first point of a welding robot is the possibility of increased productivity. In short, it means that because the robot welder has a higher arc time, it will be able to produce more efficiently than conventional welding done by hand.
Improvements in working conditions for workers
One of the other benefits of a collaborative welding robot, is that it alleviates awkward positions for the worker. The worker won’t have to be fixed in a less than ideal position for extended periods of time but will only have to feed the items momentarily and press a few buttons.
Smaller space requirements
Traditional robot cells require a lot of physical space in a production. Welding cobots however, have evolved to require less space, thus providing more flexibility for companies.
Uniformity in production
The steady hand of the robot will produce incredibly even and uniform welds. Even the steadiest welder will not be able to produce similar results, not to mention the patience and focus required.
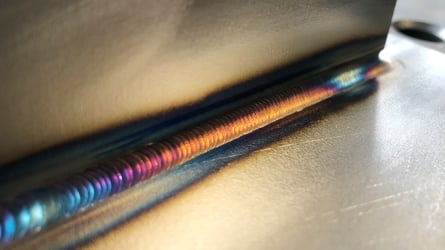
What type of ROI can you expect from a welding cobot?
One of the most common measurements for efficiency in welding is arc time. Arc time defines how long a given welder has an active arc. Given any typical welding process performed manually, a welder might produce an arc time of about 15%. This is primarily due to the physical limitations of manual labour, where breaks are required and necessary. This is due to awkward postures, fumes developed by welding and light radiation among other things. A welding cobot however, will weld as efficiently as you let it. From our experience, we often see an increase to 50% arc time. This has a very direct impact on productivity and thus on the ROI, if you can utilize the full potential of the machine.
This also makes it difficult to predict how much of an increase in productivity you will see, when you start welding with a welding cobot, because it will always depend on how much you will be able to utilize the capacity of the robot.
What is the price of a welding robot?
The price of a welding robot will depend largely on which configuration you chose. Different needs require different tools and the RBCobot-package comes with a few different options. We recommend that you reach out to us, to get a quote.